1. 前言
随着半导体、液晶制造设备为代表的高清洁度需求,以及HDD的记录密度的提升,对清洁设备的需求也在扩大,无尘室内置的搬送手臂的需求也急剧升高。在这些搬送手臂中所使用的机构是,由以矢量机器人为代表的回转机构、直交机器人中的直动机构、亦或这些组合机构所构成。
回转机构在作为发生源的驱动、支持部分容易通过油封等方法进行密封,因此有高清洁度的优点。但是从节省空间的观点来看,直动机构有利的情况较多,特别是在用于升降动作的升降台中使用了直动机构。(无尘室的单位面积成本非常高,因此节省空间化与清洁化同样重要。)
这里针对通过直动机构驱动装置来实现清洁搬运手臂的的现状与展望进行介绍。。
2.清洁搬运手臂的必要特性
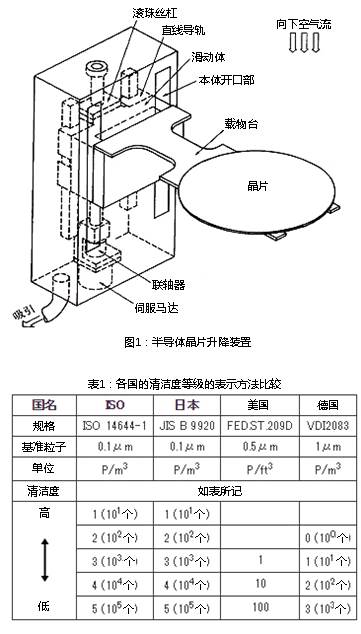
(1) 低发尘
花工夫在晶片面上产生低流动来创造清洁环境,但是由于周边物件扰乱空气,使得升降台的一部分发尘到达晶片的表面。升降台的发尘要求ISO等级2~3*)。
液晶相关设备的情况下要求ISO等级4~5。
*) 清洁度基准粒子直径(评价的最小粒子直径)和其粒子浓度来表示,需要注意以前各国的基准未统一。现在由ISO统一了规格,JIS是以ISO为标准的(参照表1).其中ISO等级2~3是“1m3的空间中存在直径0.1μm以上的粒子100~1000个以下”的意思,相同的测定值由FED表示的话就记成等级1。( 根据FED.ST.209D,等级1 = 0.5μm粒子1个 /ft3 = 0.1μm 粒子35个/ft3= 0.1μm 粒子1000 个/m3(1ft3=0.0283m3)
(2) 低振动
末端作用部的晶片抓取部单是搭载晶片就有许多抓取方式。以下是吸着方式的缺点,伴随吸着/放开的发尘无法避免、卡盘的开关需要时间这些问题的解决和抓取方式固有的弱点不抗振动的缺点,需要通过驱动装置的进步来改善。
搬运手臂中的晶片的位置偏移会引起发尘以及晶片表面的划伤,因此决不能发生(一旦发生偏移在交接晶片会将偏移量这部分推回使得再次发生偏移)。抓取方式的晶片所受的抓取力仅与晶片表面的摩擦系数有关所以对振动非常敏感。一般要求振动加速度在0.1G 以下(rms),但这也包含了启动/停止时的加减速,抓取方法也是对动作节拍自身有界限的一种方式。
3. 驱动装置的清洁度评价方法
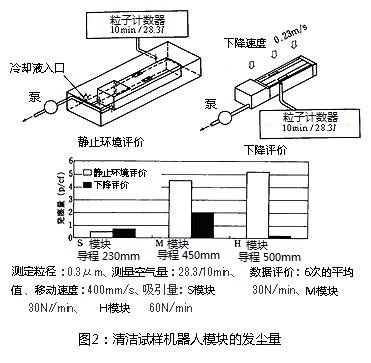
图2是本公司的直动驱动装置清洁式样XY模块3个机种用2种评价方法测定发尘量的结果。可搭载的质量从大到小依次为H、M、S模块。
低流动评价是假定在需要高清洁度的使用环境下,在驱动装置的发尘部位测定清洁度的一种评价方式(本数据是滑动平台侧面最大发尘部所测得)。另一方面,静止环境评价是将驱动装置装入盒子中,消除除样品的空气流和后述的吸引空气流、以及驱动装置的运动所产生的空气流意外的外在因素,意在捕捉驱动装置全体的发尘的一种评价方式。
低流动评价方式由捕捉局部的发尘来大约测定发尘量,但实际上起了反效果。推测是因为样品位置的发尘已经发生了扩散。测定结果受发尘部位和样品管端的距离、方向的影响,且局部存在发尘处的情况下会容易产生较大误差,这是这种评价方式的缺点。从能判断发尘处来看是个好方法,但作为驱动装置的性能评价来使用时,必须充分注意设定条件。
静止环境评价因为没有以上问题能进行高可靠性的发尘量评价,因此之后的评价都以此进行,这种评价方式是NSK评价方式。但是需要注意这种评价的测量结果导致末端作用部的清洁度会有极大的发尘量(特别是在低流动环境下末端作用部的清洁度将会有完全不同的结果)。
无论如何都可知直动驱动装置的清洁度非常优异。接下来说明提高清洁度的构造。
4. 清洁化构造
4.1. 基本构造
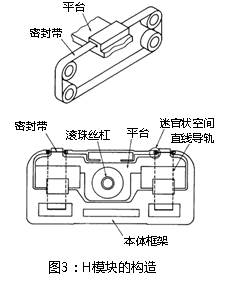
4.2. 润滑脂
滚珠丝杠、直线导轨、轴承的润滑所使用的润滑脂是主要的发尘源。图4显示了滚珠丝杠涂布不同润滑脂时的的发尘量。含氟系润滑脂广发使用于真空环境,因其粘度高发尘量少也可用于清洁环境。经过一段时间后的发尘量是一般润滑脂的1/10。
但是与图2相比,发尘量达到了20倍。理由如下所述,因吸引效果强大所致。再者,本测定是密闭空间下的发尘量,可认为与实际使用的开放空间相比值更低。
LG2润滑脂是本公司研发的清洁用润滑脂,与含氟系润滑脂有相同的发尘量。并且滚珠丝杠螺母两端设计有迷宫密封圈使得发尘量低减至1/10 。
LG2润滑脂的特点正是含氟系润滑脂的缺点。“润滑性能差”“动摩擦力矩大”“防锈能力差”这些方面上提高至与一般润滑脂同等水平。图5显示了动摩擦特性。相对于含氟系润滑脂由高基油粘度而具备低发尘特性,LG2是不依赖于基油粘度的低发尘润滑脂。
而且,对于半导体・液晶(LCD)制造设备所使用的驱动装置,正向高温、大负载的用途扩张。
这时发尘物质中存在金属元素成了大问题,为了应对此问题具有与LG2同样的发尘特性并且使用温度范围更广的低发尘・高温・低金属元素含量的清洁润滑脂式样LGU被开发及使用。

4.3. 由吸引来降低发尘量
这是由真空泵、排气扇作用于发尘源而维持负压,使得空气由外部向发尘源流入,提高清洁度的方法。其中包括滚珠丝杆螺母部分、直线导轨滑块部分独自采用吸引的方法以及驱动装置全体采用吸引的方法。
前者吸引处位于滑动侧并且由于数量众多而需要吸引气管缠绕的空间,而且由于吸引处接近于润滑脂润滑部位,所以有吸引口被润滑脂堵塞丧失机能的可能,这些都是存在的问题点。后者为防止发尘所以需要在本体的滑动开口部都生成循环的空气流,结果导致了吸引量过多的缺点。
图3的驱动装置采用了后一种方法,但在开口部使用密封皮带盖住。密封皮带的两端由滑动平台所固定,本体框架的两端设有滑轮来引导回转这样的构造。密封皮带与本体框架的沟槽部分形成的迷宫状的空间里由所产生的高速气流吸引量降低至60Nl/min(与没有密封皮带相比1/5以下)。
4.4. 由内部空气循环来降低发尘量
直动驱动产品中由本体框架所包围的直动部分有类似于活塞一样的作用,所以移动方向的前方的内部压力变高,当移动至行程末端时存在将灰尘排出的问题(活塞作用),可由以下方法减少这些影响。
(1) 直动部分的横截面积的小型化
直动部分由直线导轨滑块、滚珠丝杠螺母以及它们与工件相结合的滑动平台所组成,必须保证末端作用部的固定部的刚度。由于缩小了以上部分的横截面积,图3的产品的滑动平台的末端作用部的固定部分配置于能得到最大刚度的直线导轨的中央位置。
这与旧产品相比,旋转方向刚度提高至1.8倍的同时由于滑动平台的薄壁化使得直动部分横截面积可以从77cm 2减少至63cm2 。但是这个活塞作用在400mm/s的移动速度下以151Nl/min的速度排出灰尘,因此这也是直动驱动难以实现高清洁度的巨大原因。
(2) 本体框架两端的连通
移动平台的移动方向后方的空间与前述的相反的作用产生负压。因此与前方空间的连通能使前方空间的气压得以减小。多数的驱动装置本体框架使用了压出成形的铝材。具有确保横截面的刚性和具有多个中空部分以实现轻量化这样的形状。这些中空部分连通了滑动平台前后的移动空间,容易产生上述的作用。
5. 振动
驱动装置d振动问题大致可分为2类,需要注意它们的解决方向完全相反。
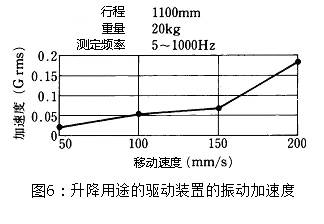
(1) 振动振幅有问题的情况
焊线工程(半导体芯片和引线框的接线工程)中,存在无法通过振动振幅来确定末端作用部的位置的问题,提高刚性、轻量化可提高固有频率有助于问题的改善。
(2) 振动加速度有问题的情况
出现于晶片搬运手臂中。降低刚性会有固有频率的下降、振动加速度的减小的倾向。但是当驱动部分的刚性比较低的时候,远位的晶片部分的振动振幅被放大,因此难以确定停止位置。重视驱动部分的刚性,末端作用部在振动加速度与振动振幅之间取得平衡,这么做比较有效。 图6显示了升降用途的驱动装置的振动加速度测定的例子。
6. 后记
清洁搬运手臂将来的需求将是“减低发尘量和减小可检出微粒的半径”以及“需求扩大的同时降低成本”。
随着半导体晶体的高集成化,同时进行着减低发尘量和减小可检出微粒的半径,就驱动部来说不久的将来会要求至0.05μm的粒子 35个/m3这种程度。在追求滚动引导型驱动装置的极致性能的同时,非接触式驱动、引导驱动方式所构成的搬运手臂在今后也可能迎来需求期。
另一方面,HDD的高密度化,LCD、PDP的普及所需要的组装・检查工程中对清洁搬运手臂的需求也在扩大,想必今后降低成本的需求也会越来越强烈。但是与一般的搬运手臂不同,清洁搬运手臂有低流动等设备方面的高价格,所以对于驱动装置的需求来说,相较于低成本化更需要能简易安装的高清洁度的产品。
无论如何期待清洁产品市场的扩大的同时,清洁搬运手臂技术与现今依赖于清洁空气供给的装置保持同一水准的清洁度,日益向有竞争力的性能水平的产品成熟发展。